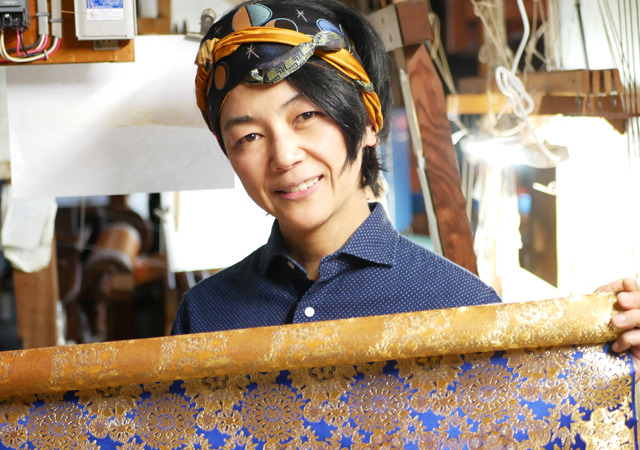
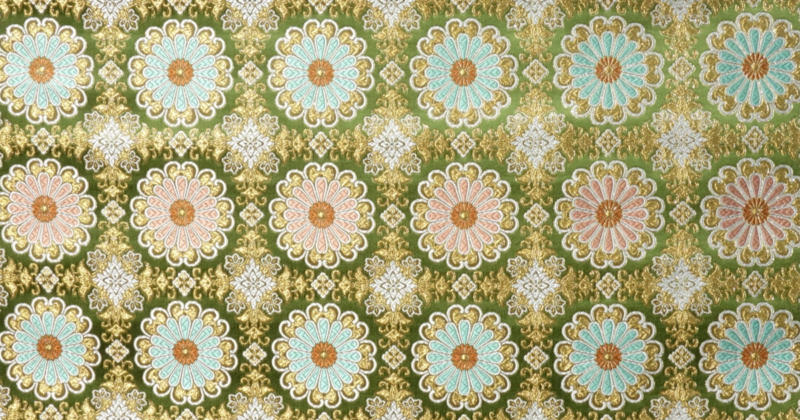
History and features of Nishijin textiles
What is Nishijin weaving?
Nishijin textiles are woven by weavers belonging to the Nishijin Textile Industry Association. The north-western part of Kyoto (Kamigyo and Kita wards) is known as Nishijin, an area where textile manufacturers have gathered since the Heian period (794-1185).
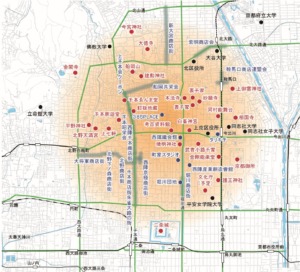
Weaving of fine textiles began in Kyoto with the introduction of techniques from Tang China in the Kofun period. During the Onin War in Kyoto in the Muromachi period (1336-1573), the area where Yamana Munetada, a general in the Western Army, set up the ‘Western Camp’ came to be known as the ‘Nishijin’ area and was given the name Nishijin-ori. The general of the ‘eastern camp’ was Hosokawa Katsumoto. The production process of Nishijin-ori varies slightly from weaver to weaver, but 12 varieties of Nishijin-ori were designated by the national government as traditional Nishijin textiles as of 26 February 1976. Nishijin-ori weavers continue to produce textiles today, each with its own individual character.
Features and products
Nishijin weaving,
- Tsumegaki Hontsuzure-ori : Weave complex fabrics by sawing the tips of the fingers with a file and using the tips of the fingers as a reed to draw in the weft threads, without relying on pattern paper data.
- Warp brocade : The warp threads are used to produce the ground and pattern.
- Weft brocade : A combination of weft yarns produces a rich pattern. Click here to see our textiles.
- Donsu : Thick and lustrous satin.
- Shuchin : Various weave patterns are produced by using weft yarns on 4 rugs. Click here to see our woven fabrics.
- Shoha : Use high-twisted warp and weft yarns and weave weave patterns with the weft yarns.
- Huutsuu : The warp and weft yarns are of different colours and the same pattern is shown in opposite shades on the front and back sides, also known as day and night weaving.
- Mojiri-ori : A coarse weave in which two warp threads are twisted and interwoven with the weft threads, used to weave transparent fabrics such as ra, ro and gauze.
- Honshibo-ori : A weave in which the twisted yarns are twisted in an ingenious way so that a crease appears.
- Velvet : Hand-cut velvet is woven in Nishijin.
- Kasuri-ori : fabrics using warp and weft yarns dyed to produce a pattern when woven.
- Tsumugi : Textiles that use knotted yarns to create a unique texture.
As mentioned above, a wide variety of weaving methods have been developed. As the threads are dyed in advance before weaving, one of the appeals of this weaving method is that it produces more complex and heavy fabrics than the general dyeing method of post-dyeing. Weaves range in structure from plain weave to complex luo, in yarn from synthetic, cotton, silk and advanced fibres, and in design from simple to elaborate.
Nishijin” and “Nishijin-ori” are protected by a registered trade mark owned by the Nishijin Textile Industry Association.
History of Nishijin textiles
Its origins date back to the Kofun period between the 5th and 6th centuries. Sericulture and silk weaving techniques, introduced by the migrant Hata clan, developed in government-run weaving workshops during the Heian period (794-1185), forming Oribe-cho, a town where artisans gathered. During the Muromachi period, the silk and twill produced in Ootonericho were prized for their high quality, and an organisation known as Ootoneriza was born. After the Onin War, artisans who had taken refuge in Sakai, Osaka, returned to Kyoto and resumed the weaving industry in the Nishijin area, establishing the technique of mon-ori.
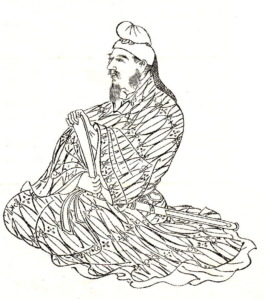
Heian period (794-1185).
During the Kofun period (794-1185), the Hata clan, who came to Japan from the Kofun period, settled in the area around Uzumasa in Kyoto and introduced sericulture and silk weaving techniques. In the Heian period (794-1185), a government-run textile workshop was established to weave and dye brocade, twill, pongee, luo and other fabrics for the Imperial Court, and began to produce high-quality textiles.
The Imperial Court set up an organisation called Oribe-ji (an institution belonging to the Ministry of Finance under the Ritsuryo system) under the government to produce brocade, twill, pongee and luo for the Imperial Court, with artisans inheriting silk weaving techniques.
Muromachi period (1336-1573)
The silk and twill dyed and woven products produced in Ootonericho were of high quality and highly prized, giving rise to an organisation called Ootoneriza in the Muromachi period. This organisation responded to the demand for high-quality textiles from the imperial court’s built-in dormitories, but also took orders from ordinary court nobles and samurai families. The Ootoneriza appears to have been active in the area around today’s Kamichoja-cho, Kamigyo-ku, Kyoto.
Onin War (1467-1477)
The fires caused by this war destroyed the Ootonericho area, but around ten years after the war subsided, artisans who had taken refuge in Sakai, Osaka, returned to Kyoto and resumed their weaving business in the Shirakumo village near Ootonericho (near present-day Shinmachi Imadegawa-agaru, Kamigyo-ku) and the Omiya Imadegawa area. The name Nishijin-ori is a place name derived from Nishi-no-jin, the site of the headquarters of the Western Army.
Weaving technique
With the introduction of the mon-ori technique Sorahikibata, mon-ori flourished, laying the foundations for the high-class silk weaving Nishijin-ori and establishing Nishijin as a production area. After the Meiji Restoration, Nishijin sent students to Lyon, France, and introduced the advanced technology of Jacquard. This led to successful modernisation. In modern times, the air-drawn loom (see image below) is only revived in the Nishijin Weaving Hall, but in general weaving is done on hand looms, power looms, rapier looms and air-jet looms.
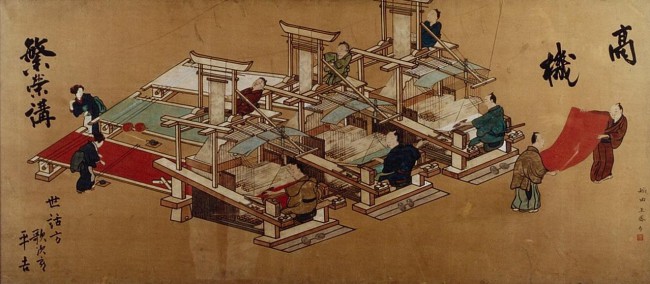
Present day
Nishijin textiles are characterised by high-mix, low-volume production and are produced not only for religious gold brocade and obi, but also for apparel and interior applications.
Adaptation to modern times
Even today, Nishijin brocade is characterised by high-mix, low-volume production: each of the nearly 300 weavers uses its own special technique and materials to produce not only the famous obi, religious brocade, neckties, outer garments, umbrellas and shawls, but also new products for interior decoration. In Nishijin, we keep traditional materials and techniques, while developing new designs and products for new uses.
Production process (in our case)
Design
Nishijin weaving is a method of weaving fabric using yarn dyed in advance, rather than dyeing the woven fabric. Therefore, it is necessary to plan a design that envisages the image of the finished weave. The draughtsman receives the order from the customer and draws the design in the customer’s image. This may be redone a number of times in order to match the design.
Design drawing
Next, a design is drawn up. This is called a design drawing. The enlarged design is projected onto a sheet of paper similar to a grid (not square, but with squares corresponding to the longitudinal ratio of the textile to be woven), and the pattern is copied with a pencil. The squares were used to indicate the combination of warp and weft threads on the jacquard loom. In addition to the thread colours, the pattern design chart also contains various information and instructions designed to make the fabric easier to weave. Nowadays, the drawings are often made using digital data such as Photoshop, but even though they are digital, they are like rough dots, so each dot is drawn one by one.
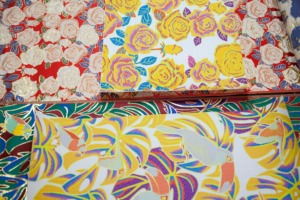
Monhori (engraving)
In order for the weaving machine to read the information on the design chart and weave the pattern according to the design, a process called monhori (engraving) is carried out. Monhori is a method of specifying information such as the position of the warp and weft threads up and down and the combination of coloured threads, square by square, by punching holes in a piece of paper called mongami. Holes were punched precisely using a machine such as a piano type mon-gami machine. Nowadays, computer graphic processing is widespread and crest paper is made as GGS data, rather than on actual paper. The picture below shows a small tissue pattern paper for our hand weaving and pre-machining machines. This does not contain enough information for weaving, so holes are punched by hand.
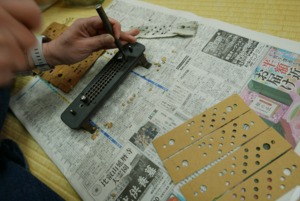
Twisted yarn
Preparation of silk threads. The silk is put through a process called twisting(nenshi). This involves twisting several silk yarns together and adjusting the thickness of the yarn. Twisting yarns of various thicknesses gives the Nishijin brocade its unique texture. Silk yarns of various thicknesses are used according to the product to be woven.
Thread dyeing
Silk yarns are sent out to be kneaded (refining). The dyer removes impurities from the silk yarn (natural impurities such as fibroin, a protein and sericin, a glue-like protein and wax) to produce a shiny white yarn. The yarn is then dyed to the colour ordered. As we dye many colours, we dye in small quantities, so the dyeing artisan’s intuition is very important.
Warp and weft reeling
Warp and weft yarns are wound onto a thread frame. In the past, the yarn was wound manually, but nowadays mechanical reeling is the norm.
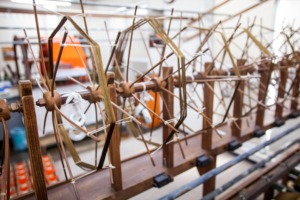
Warp preparation
The thousands of warp threads required for weaving are wound onto a round tube called a ‘chikiri’ (beam), which is set on the loom, so that they can be woven in the required length. This process is called seikei.
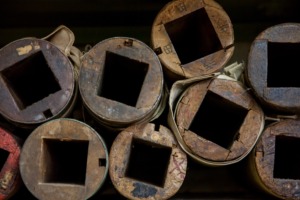
Heddles
When the warp threads are set on the loom, they are threaded through the part called the heddle, which is made of thread and wire. This is an important step in weaving the warp and weft yarns into the intricate patterns of Nishijin brocade.
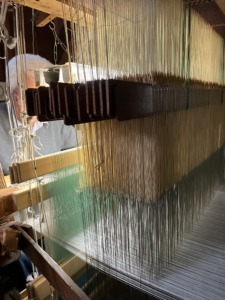
Weft winding
Yarn is wound around a thin bamboo-like tube for weaving into a weft.
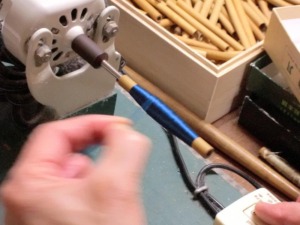
Weaving
Weaving is done on hand looms, power looms, spelling looms, rapier looms and air-jet looms. Rapier and air-jet looms are used. Although rapiers and air jets have become popular in recent years, delicate weaving using a lot of silk, such as gold brocade, requires slow weaving on a hand loom or power loom.
Through these processes, the Nishijin brocade has brought its delicate beauty to the world. A fusion of traditional techniques and modern needs, Nishijin textiles continue to be a symbol of Japanese culture and are still loved by many people.
References: Nishijin Tengu Writing Stories: A Personal History of Nishijin, Koma Toshiro.